How a One Touch System Can Boost Your Body Shop’s Efficiency
Every shop is looking to increase its efficiency, whether by equipment or process. It’s crucial to ensure that the floor layout is set up in the most efficient way possible to help turn out more jobs per day. A disorganized layout can cause bottlenecks and add additional time to jobs that otherwise would not exist. With that being said, it can sometimes be tricky to understand what step in the process is taking longer than another.
To get ahead of potential production issues, we’d have to go back to the beginning. Before setting up a new finishing system in a body shop, it’s important to evaluate what’s already there. Oftentimes, there is pre-existing equipment that needs to be worked around. Placing any new equipment, such as a paint booth, mix room, or prep station, must be strategically done to ensure it doesn’t disrupt the painting process, but rather enhance it. That’s where the one touch system comes into play.
What is a One Touch System?
A one touch system isn’t actually a physical system, but rather a method that can be implemented in any shop with the proper setup. Essentially, one touch eliminates time during the refinishing process by processing full jobs at one time by doing jamb work and exterior, also handling multiple RO’s in a single booth cycle by painting all parts off the vehicle. Let’s get into how that works.
Imagine you’re painting in a shop that has a prep station, mix room, and paint booth. A refinishing job comes in for a standard sedan needing its bumper, hood, and fender touched up. Some shops choose to leave the part on the vehicle rather than disassembling it. While this still gets the job done, it can triple the time of a job by having to repeat the prep, taping, painting, and drying process for each area of the car.
Now let’s explore how this process would look if the shop followed up a one touch system. With this setup, the bumper, hood, and fender would all be removed from the car and moved into the paint shop at one time to be prepped, painted, and dried simultaneously. While it is slightly more up-front work to remove all parts from the vehicle, it saves time for the overall job as to complete all refinishing at the same time.
The Benefits of Implementing One Touch
While the above scenario shows the benefits of one touch for a single job, the same process can be applied to work multiple jobs simultaneously—therefore, saving time and material. When you’re working multiple paint jobs a day, it’s easier and more efficient to mix clear and coatings only once or twice rather than for each individual paint job. For example, taking apart only the parts of the cars that need to be coated and bringing them into the booth, rather than one car at a time.
To further shop efficiency, we recommend having a mix room that is attached to a paint booth. An attached mix room decreases the time it takes between going to and from the booth, plus there’s less chance of contamination than entering the booth directly from the shop. Further, it helps to streamline the overall refinishing process.
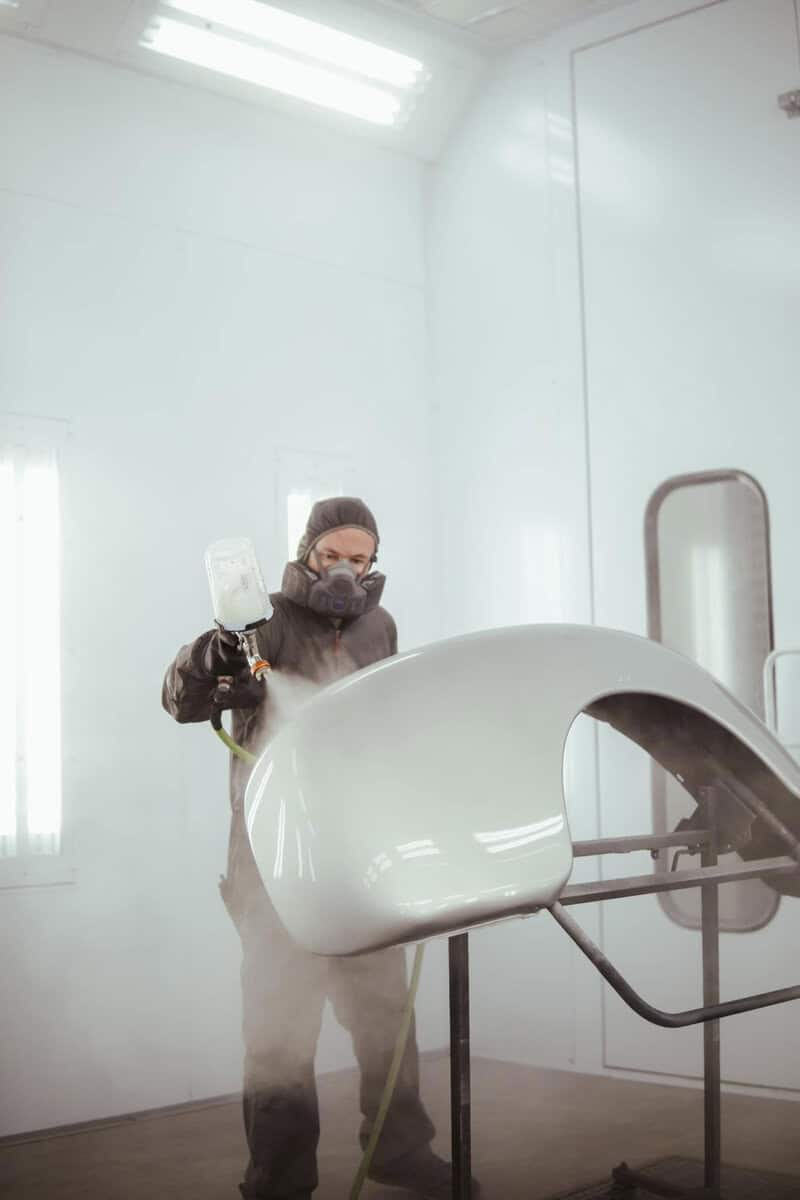
The Ideal Finishing System for One Touch
Check out this recent shot from Leonardtown Collision Center in Maryland on a classic job they recently had in their custom double booth. With 12’ of interior height from an Accudraft Italia Alto and enough room for any parts they come across, every job can be done in a one touch setup in one booth cycle, every time. They also had a connecting Accudraft Magnum 5000 Prep Station to ensure a seamless transition between prep and painting work.
Increase Your Body Shop’s Efficiency with Accudraft
If you’re looking to increase your body shop’s efficiency, Accudraft is the right partner for you. We’re not simply a paint booth manufacturer, we go above and beyond to ensure our finishing system is the right fit for your production line. From planning to installation to ongoing maintenance, we’re with you every step of the way. Contact us today.